BLOG
August 29 2024
back to listSuccess story: Cleaning flour silos
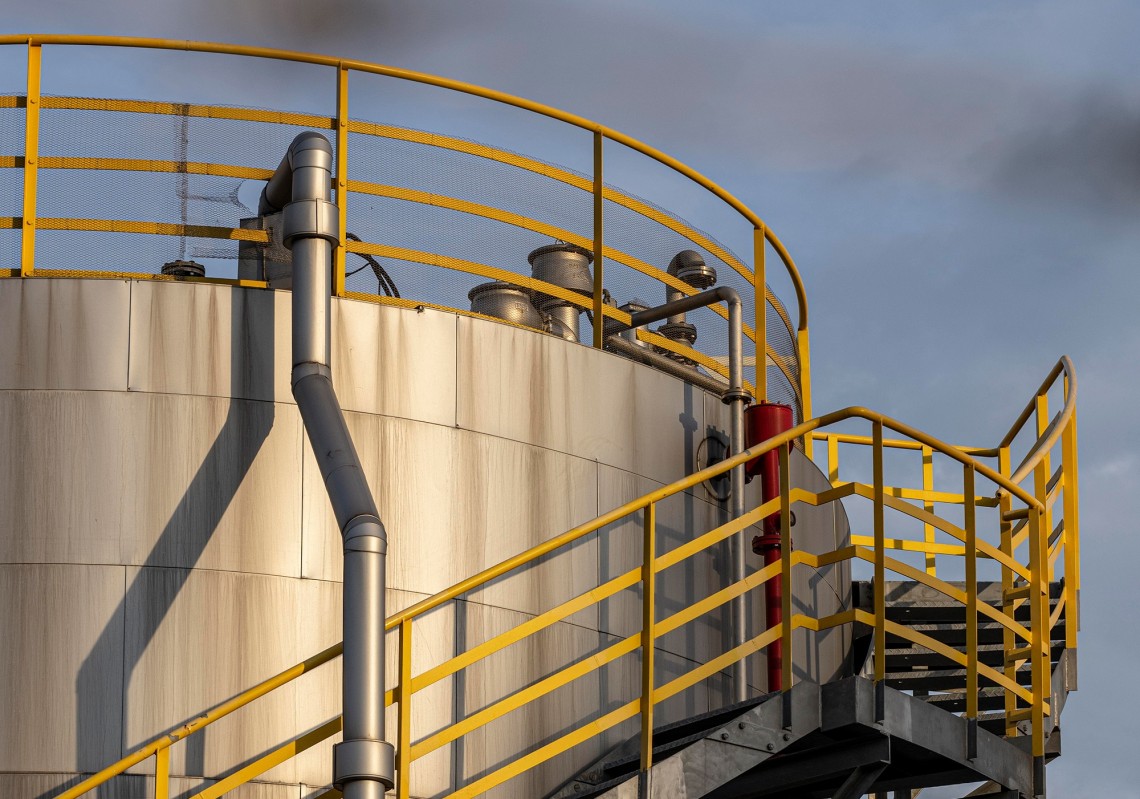
Initial Situation:
Cylindrical flour silos, approximately 3.5 m in diameter and 33 m in height, without internal structures, with uninsulated aluminum walls. Each silo has a conical geometry and a flat top with an eccentric manhole.
Production operates 24 hours a day throughout the year, so each silo is periodically filled completely with flour and then emptied continuously or intermittently, depending on process requirements. As a result, the interior of the tank becomes irregularly contaminated with product residue deposits. These contaminants accumulate at various points and levels. In particular, lumps of flour form at all heights of the silo walls, which, once the level has risen to a certain point, tend to fall uncontrollably. This then causes recurring blockages, leading to stoppages in the flour transport and production facilities. This results in costly production downtime for repairs.
For decades, the cleaning process involved hired cleaning workers/industrial climbers, equipped with manual lifting devices and supervised by a safety supervisor, entering the silos to clean them. Flour residues, ranging from light dust to heavily embedded or sticky residues, were removed with brushes or brooms for light contamination or with spatulas and scrapers, miner-style, for more difficult residues. This procedure not only imposed extremely high physical and mental stress on the workers, who had to be provided with breathable air, but the cleaning also took several hours or even an entire day. Furthermore, the efficiency of the cleaning varied from worker to worker, and the results were not repeatable. Due to the eccentric inspection opening, the placement of safety and lifting devices for the cleaning workers was complicated and time-consuming.
Objective:
The company was looking for a modern water-based cleaning process with reliable and repeatable results. An essential prerequisite was strict compliance with all customer requirements and regulations regarding food safety and hygienic production environment. However, profitability was also of great importance to the customer, meaning the minimization of cleaning times, cleaning agents, services, and auxiliary materials, as well as the sustainability of the system.
Analysis:
Aligning these engineering considerations with the customer's requirements led to the identification of the most suitable type of cleaner. Fixed or static nozzles were excluded, as they are designed for easily cleanable liquids and not for the typical contamination level of flour silos. Rotating devices would have been powerful enough to work in a smaller silo, but not for the application in question.
An orbital cleaning device proved to be optimal for the application, as it has circular nozzles that generate ideal and highly concentrated jets that cover the entire surface to be cleaned.
Proposal:
Considering an installation height of over 33 m, an orbital device with four 7 mm nozzles was placed in each silo. This device discharges approximately 12 m³/h of cleaning water at a working pressure of 5 bar.
To test the selected 4-nozzle orbital device, it was connected via a hose to a centrifugal pump placed at the bottom of the silo, then eccentrically introduced into the silo and positioned at a submersion depth of 2500 mm with a lateral distance to the wall of 500 mm.
Results:
After placing the device, the cleaning process was initiated and monitored. When the process stopped after three minutes, a large portion of the adhered contamination, even critical, had already been removed from the surfaces of the silo that were covered by the powerful cleaning jets. This cleaning result, obtained just a few minutes later, confirmed that the chosen path was the correct one.
After a total cleaning of just 15 minutes, all contaminants were removed, especially the more resistant flour deposits. Despite the eccentric position of the cleaner, no oscillating movement occurred in the silo, thanks to the balanced design of the cleaner. The jets generated a pattern that covered the entire surface of the silo, even in the deepest areas.
Conclusion:
The final laboratory analysis of the samples from the surface of the silo confirmed that the desired and expected results had been achieved. The water-based cleaning process selected and described in this article is repeatable under the determined conditions and achieves the desired result efficiently and effectively. Furthermore, the defined process allows for intermediate cleaning to be performed at any time in case contamination increases. Expensive external cleaning specialists are no longer needed, as water cleaning can be easily carried out by the client's own staff without costly plant shutdown.