BLOG
October 21 2024
back to listComparative analysis of heat exchange technologies
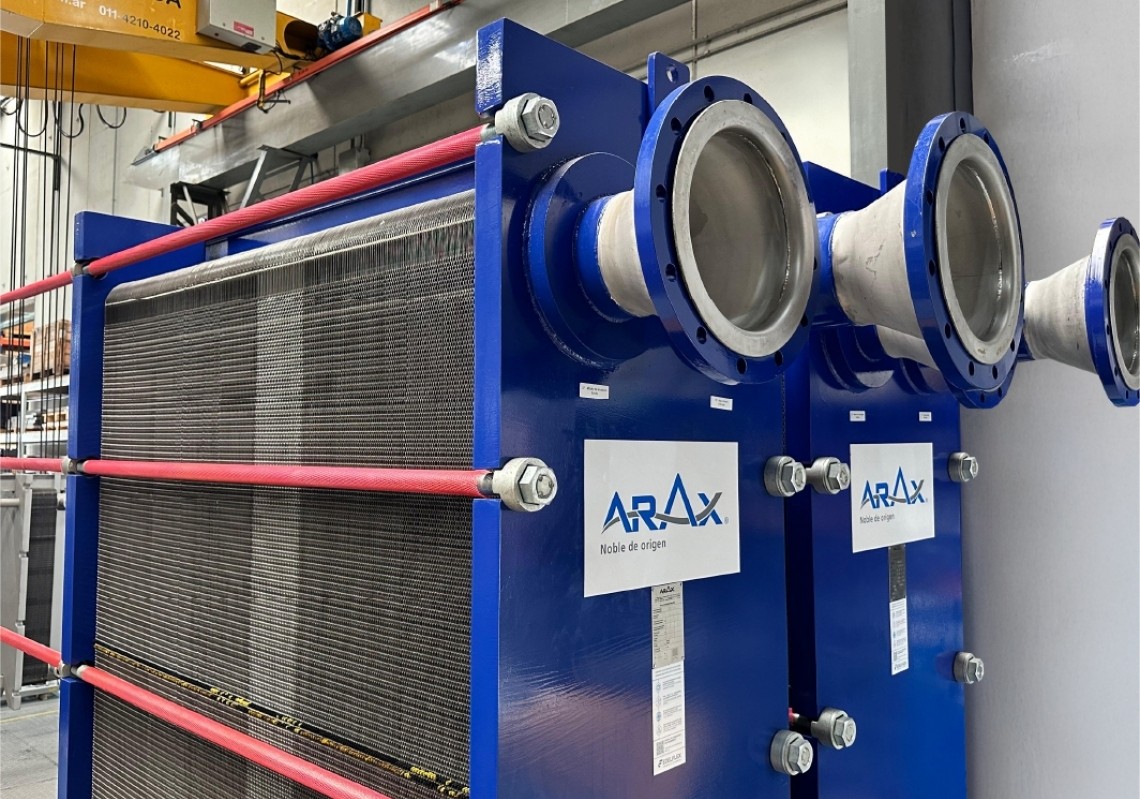
Heat exchangers are key components in a wide range of industries, as they facilitate heat transfer between two fluids, optimizing thermal processes and improving energy efficiency. These devices are designed flexibly to adapt to different needs, and depending on the technology used, they can differ significantly in terms of design, efficiency, operational capacity, and specific applications.
Among the most common heat exchanger technologies are:
- Plate and gasket
- Brazed plates
- Welded plates
- Shell and plate
- Shell and tube
The main difference between these technologies lies in the maximum process conditions that each type can withstand, such as temperature, pressure, and the nature of the fluids.
PLATE AND GASKET HEAT EXCHANGERS
Design:
Plate heat exchangers consist of a pack of thin corrugated metal plates, arranged one on top of the other and separated by elastomeric material gaskets. Fluids flow through alternate channels formed between the plates. This set of plates is contained in a frame, which includes connections for the pipes.
Heat Transfer:
Heat transfer occurs through the walls of the plates, achieving high thermal efficiency due to the large contact surface available for heat exchange.
Advantages:
- High thermal efficiency due to the large transfer area.
- Easy disassembly for cleaning and maintenance.
- Compact and lightweight design, ideal for tight spaces.
Disadvantages:
- Gaskets may deteriorate over time and under certain conditions, such as high temperatures or corrosive fluids.
- Limited for applications with high pressures or extreme temperatures.

SHELL AND TUBE HEAT EXCHANGERS
Design:
They consist of a set of tubes mounted inside a cylinder or shell. One fluid circulates inside the tubes, while the other fluid flows in counterflow through the space between the tubes and the shell, optimizing heat transfer.
Heat Transfer:
Heat exchange occurs through the walls of the tubes. The large surface area of the tubes contributes to effective thermal exchange, although not as efficient as in other more modern designs.
Advantages:
- Suitable for high pressure and temperature applications.
- Can withstand large temperature differences between the fluids.
- Can handle fluids with solid particles or high viscosities without affecting their operation.
Disadvantages:
- Lower thermal efficiency compared to plate heat exchangers.
- They are bulkier and heavier, which increases investment costs.
- Maintenance and cleaning are more complex and require more time.
SHELL AND PLATE HEAT EXCHANGERS
Design:
Combines features of plate heat exchangers and shell and tube exchangers. Uses welded plates inside a shell, eliminating the need for gaskets, which allows them to withstand more extreme pressure and temperature conditions.
Heat Transfer:
Fluids circulate through the channels between the plates, providing a more efficient thermal transfer than traditional shell and tube exchangers.
Advantages:
- Greater thermal efficiency than conventional shell and tube exchangers.
- Can withstand higher pressures and temperatures than gasketed plate exchangers, thanks to the absence of gaskets.
- Lower risk of leaks, making them more reliable under extreme conditions.
Disadvantages:
- Higher initial cost due to greater design complexity.
- More difficult maintenance compared to gasketed plate exchangers, as they cannot be easily disassembled for cleaning.